Category
- Products
- Contact us
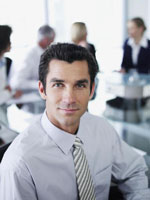
Gas Detector Supplier

Home » Application » Page 2
The online monitoring system of the sewage plant is made up of the ammonia gas detector and the alarm controller, of which the gas detector is installed on the operation site and the alarm control engine is installed in the environment for the convenience of the monitoring room's monitoring. As to the installation position of the ammonia gas detector for the sludge treatment plant, the location where ammonia gas leakage is easy to happen, or the location where the operation personnel’s operating environment will not be influenced, can be installed with the ammonia gas detector.
There is residual of hydrogen sulfide in the surroundings or workshop of the plant, which can seriously erode solid surface on various facilities. Therefore, it is necessary to give full play to the special instrument’s operating capability, and the hydrogen sulfide detector with steady performance should be put in a conspicuous place for workers. The instrument whose panel can display numbers at a far distance should be selected. In this way, precautions can be taken before entering the dangerous region.
When the hydrogen gas detector is applied to production safety, real-time monitoring should be conducted in accordance with production safety. Once the gas leakage occurs, the corresponding measures should be adopted. Personnel should be evacuated, and the leakage polluted area should be moved to the upwind position and the polluted area should be isolated to strictly limit entry and exit. Cut off all kinds of fire sources and leakage sources.
The flammable gases in oil fields are relatively complex, because these flammable gases include both class A flammable gases (lower explosive concentration limit is less than 10%), such as hydrogen, hydrogen sulfide, methane, ethane, propane, butane, ethylene, propylene, acetylene, chloroethylene, formaldehyde, methylamine, epoxyethane, coke-oven gas, water gas, natural gas, associated (-dissolved) gas, liquefied petroleum gas, etc. and class B flammable gases (lower explosive concentration limit is more than or equal to 10%), such as ammonia, carbon monoxide, carbon sulfide, producer gas and so on. Since the lower explosive concentration limit of these flammable gases are different, and some gases are negative to the sensor but some are positive to the sensor, so how to choose the range of flammable gas detector for the oilfield?
Industry: sulfur dioxide gas detector is widely used in industry, such as effluent treatment and safe production, especially downhole operation, which needs to monitor the concentration of sulfur dioxide. In addition, it is also commonly used in metal processing, pulp and paper making, cleaning and solvent extraction, as well as low-temperature cleaning industry related to sulfur dioxide.
Choose the suitable ozone generator according to the volume of the clean room. Connect the external ozone generator to the suitable position of the air sending and air return main pipeline of the HVAC system via the pipe. The PLC system can preset processing parameters, such as sterilization time. During the process of sterilization, turn off around 90% of the ventilation inlet valves and return air external discharge valves. In this way, the air in the sterilized clean room forms a circulating state via the purification system’s air channel. Every day, 1h is started for sterilization of the air, which is equal to the effect of the chemical agent fumigation and equipment surface sterilization started for 2h to 2.5h. It can also be used alone in the clean room with the return air entrance for partial sterilization.
The most commonly-seen damage caused by the oxygen concentration to the human body is caused by the pathological process of the human body caused by hypoxia. More seriously, major organs, including heart and brain, might be dead because of hypoxia. In fact, when the oxygen gas detector is used to detect the oxygen content in confined spaces, one should not only consider suffocation and shock caused by entry of personnel caused by a too low oxygen concentration. Under some conditions, the airtight space might also cause unpredictable chemical responses or intensification of combustion when the oxygen content is too high.
In order to ensure personnel, equipment and environment safety during the sulfur-containing oil-and-gas-field exploitation, development and production process, safety measures have been heavily invested for construction teams. The fixed hydrogen sulfide detector is one of the measures. Its probe is usually installed at the drill entrance, drill platform, vibrating screen, mud circulating tank, and other areas where hydrogen sulfide can easily leak out and gather. It is for the purpose of realizing all-weather continuous monitoring of the hydrogen sulfide concentration, which can prevent poisoning of the hydrogen sulfide and ensure production safety. In order to help onsite personnel to discover problems with the detector at an earlier date, ATO technicians have analyzed commonly-seen faults and their causes according to years of experience, hoping that the analysis can ensure timely onsite processing and accurate maintenance.
In fact, there are still some toxic gases, which cannot be distinguished, such as the gases (hydrogen sulfide and hydrocyanic acid), and some commonly-seen toxic gases, such as CO, NO, SO2, and chlorine. Many factors have installed the combustible gas detector for the convenience of better preventing toxic and hazardous gases from doing harm to the human body. It is suggested that industrial plants should install toxic and combustible gas detector to avoid occurrence of personnel poisoning. Toxic gases exist in production raw materials and by-products of different links. The hazardous are reflected as chronic hazards, which can cause discomfort to one's physical health. With the passage of time, the quantity of toxic gases inhaled, when reaching certain quantity, will cause poisoning. Some toxic gases are even more dangerous. Personnel once exposed to these gases will be poisoned, suffering slight disability, cancerization, or even death.
Ammonia gas detector is more and more widely applied to breeding industry chain. Since chicken manure may produce a lot of ammonia in the chicken house, when the content of ammonia in the air of chicken house reaches 20 ppm (equivalent to 15.2 mg/m³) and lasts for more than 6 weeks, it will cause pneumonemia, edema, loss of appetite, decrease of egg-laying ability to chickens and make them vulnerable to diseases; when the content of ammonia reaches 50ppm, there will be laryngeal edema, necrotizing bronchitis, pneumorrhagia, decrease of respiratory frequency and even death in chickens several days later. Therefore, the ammonia concentration in the chicken house should be controlled below 20 ppm.