Category
- Products
- Contact us
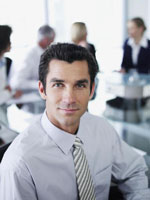
Gas Detector Supplier

Home » Solutions
In the process of using a gas detector, it could be caused by a malfunction in the gas detector, or other causes, and the tests are not accurate, and the instrument is one of them, so what are the reasons why the detectors have been speaking, and how do we fix it?
The production equipment producing hydrogen sulfide should be closed as far as possible, and the automatic alarm device of hydrogen sulfide gas detector should be set (the concentration of hydrogen sulfide in dangerous places cannot be judged according to the smell, and hydrogen sulfide will lead to olfactory paralysis when it reaches a certain concentration).
If the sensor is used for a long time, the measured value might have certain error. It is necessary to confirm with the plant about whether the sensor can be used continuously. If the service life of the sensor is nearly expired, the sensor might be serviceable after completion of calibration, and the sensor would be unable to use for a long time. Then, it is suggested that a new sensor should be adopted.
The detection error of the instrument refers to the error between indication and the set value. The alarm point of the instrument is set at 24µmol/mol, and the 28µmol/mol standard gas is injected into the instrument to read the alarm level. Repeat this step for three times and take the average of the reading of the three times as the alarm level of the instrument. Calculate the instrument's alarm error, and judge whether the detector is qualified.
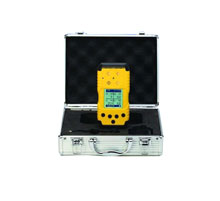
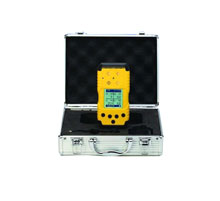
The gas detection probe should be located 1m nearby the valve, pipeline interface, outlet or places easy to have gas leakage, but should not influence operation of other equipment. Besides, the location of the gas detection probe should have no huge vibration and be steady, and the high-temperature, high-moisture and electromagnetic environment should be avoided. The external influence should be avoided. For example, water spray and oil might cause mechanical damage. The installation position should be as close to the personnel as possible for the convenience of maintenance and demarcation.
The gas detector might be in fault because of improper operation or other causes. Consequently, the detection data might be inaccurate. Continuing alarm of the gas detector is one of these faults. Then, what are causes of continuing alarm of the gas detector?
It should be confirmed that whether zero-point calibration or target-point calibration is necessary for the instrument. If zero-point calibration is conducted on the occasions with the target gases to be measured, the low-concentration gases might fail to be detected. If the target-point-calibration is conducted on occasions with target gases to be measured, but the calibrated concentration value and the actual concentration value are inconsistent with each other, the instrument value might fluctuate significantly or the numerical value detected might be small. Under these two conditions, the ex-factory operations can be resumed as a solution.
First, use the calibration device for calibration. Usethe ozone detector designed based on the ultraviolet light method to choose tentest points on the ozone detector for comparison. Control the error scopewithin ±1% to be qualified.Second, use the chemical titration for calibration. Theinternationally-acknowledged chemical method, namely potassium iodide andsodium thiosulfate titration for detection of the ozone concentration. We willalso select ten test points, and compare them with ten points tested by thechemical titration using the ozone detector.
Soak the ozone oxidization color-variable reagent in the carrier as the reactant. Seal it in the glass tube as the detector tube. In the use process, cut the two ends of the detector tube apart. Connect the aspirator to the outlet of the detector tube to take in a fixed quantity of ozone. The ozone concentration and the color-changing length of the reactant within the detector tube are in direct proportion to each other. The concentration value is read by the scale interval.
Under general conditions, the gas density should be smaller than the air density. The oxygen detector should be installed above the region with potential leakage sources. If the gas density is larger than the air density, the detector should be installed 30cm to 60cm above the ground. As to gases whose density is similar to the air, the detector should be installed closer to the operation space (namely the respiration area) of onsite personnel.
Precision is an important performance index of the gas detector and an important factor influencing precision of measurement results of the gas detector. According to national standards, precision of the gas detector should be ±3% of the full range. The gas detector with a higher precision can achieve ±1% of the full range. The higher the precision is, the better the performance of the gas detector is.
The service life of the gas detector is mainly decidedby its main component, gas sensor. As we know, there is not a sensor which candetect all kinds of gases and satisfy all kinds of requirements. The sensor todetect different gases and for different environments is different, which canbe generally divided into the sensor to detect the toxic gas concentration andthe sensor to detect the flammable gas explosion concentration. The sensor used to measure theconcentration of toxic gases is mostly an electrochemical sensor. As a sensormade based on the electrochemical principle, it is mainly influenced byelectrolyte in terms of its service life. Under an ideal environment, theelectrolyte will be consumed to a level that most sensors cannot work normally.Therefore, the service life of electrochemical sensors is two to three years.