Category
- Products
- Contact us
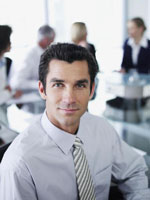
Gas Detector Supplier

Home » Gas Detector » Methods for Troubleshooting of the Gas Detector
Methods for Troubleshooting of the Gas Detector
urrently, gas detectors have found wide applications in manufacturing activities. The commonly-seen gas detectors include the four-in-one gas detector, portable inflammable gas detector, portable TVOC detector, oxygen gas detector, etc. Today, ATO technicians would like to share with you methods for troubleshooting of the gas detector.
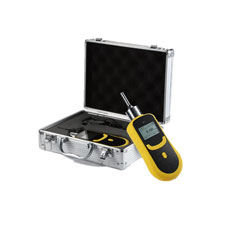
Knocking and hand-pressing method
The instrument might not work well at times. The phenomenon is mostly caused by poor contact or cold solder joint. Under the condition, knocking and hand-pressing are required. Knocking is to gently knock on plug-in boards or components using the small rubber hammer or other objects to see whether mistakes or halts will be caused.
The so-called hand-pressing method is to press on plug-in components, plugs and seats with hands for firming after power off. Then, power on to see whether the existing faults are eliminated. If the machine shell is normal by the first knocking but abnormal by the second knocking, you should try again after re-plug all contacts firmly. If this method does not work, you should find out other methods.
Observation method
Observation means inspection by vision, smell and touch. Sometimes, the damaged components might change their color, have bubbles or be found with burned spots. The burned electric components might have some special gases. The chip after short circuit will be very hot. When there is cold solder joint or loose weld, you can observe it by your naked eyes.
Exclusion method
The exclusion method is a method which judges faults by unplugging some plug-in boards and devices. When the instrument resumes its normal operation after a plug-in board or device is removed, it means that the board or the device is the fault.
Comparison method
There should be two instruments of the same type. One of them can operate normally. Use of this method requires other necessary devices, such as multimeters and oscillators. Classified by attributes, there is voltage comparison, waveform comparison, static impedance comparison, output result comparison and current comparison.
As to steps of the comparison method, first let the normal instrument and the instrument at fault operate under the same situations. After that, some dot signals are compared and two groups of signals are compared. If there is any difference, the fault can be identified. This method has a high requirement of maintenance personnel’s knowledge and skills.
Temperature rise and fall
Sometimes, the instrument might be in fault for working for a long period of time or in summer when the operating environment temperature is high. Every part is normal when the instrument is turned off for inspection, and the instrument can operate normally after a period of time. The phenomenon is caused in poor performance of some IC pieces or components, which cannot meet requirements of the high-temperature resistance index. In order to find out the causes, you can adopt the temperature rise and fall method.
As to the temperature fall, when the fault occurs, use the cotton fiber to wipe the part in fault using the anhydrous alcohol to cool down the part and observe whether the fault is removed. As to temperature rise, it means the ambient temperature is artificially increased. For example, the electric soldering iron can be put nearby the parts with suspicious points (ensure that the temperature does not rise too high to cause damage of normal components) to see whether the fault occurs.
Post a Comment:
You may also like: