Category
- Products
- Contact us
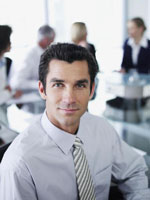
Gas Detector Supplier

Pump Gas Detector Troubleshooting
Fault 1: Failure to detect the gas at low concentrations.
Solution: Check whether the pump works and whether there are minor vibrations when the pump works normally. Use the finger to block the outlet for two seconds and one can perceive obvious suction. Then, check whether the inlet of the filter is blocked or whether the connection fails to ensure good sealing, thus resulting in gas leakage and lack of suction.
Pump in the ammonia gas to calibrate the zero point or calibrate the zero point in the clean water. Immediately detect after calibration.
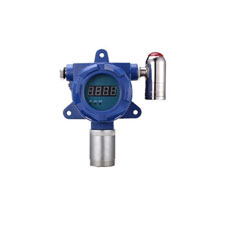
If the gas cannot yet be detected after zero-point detection, the ex-factory setting should be restored.
If the gas cannot be detected even after recovery of the ex-factory setting, the nitrogen can be pumped in or the zero-point calibration can be conducted in the clean air. Detect immediately after calibration.
Detect whether the connection line of the sensor is manually damaged or poorly connected. If the gas cannot yet be detected after all the above steps, you should confirm whether there are other gases detected onsite or whether the concentration of the detected gases is very low. If the concentration is lower than the lower limit, the target gas would be unable to detect.
Fault 2: There are no target gases to be detected in the air, but there are huge fluctuations or chaotic bounces.
Solution: That the zero-point fluctuation is smaller than 1% of the maximum range for a short period of time is a normal phenomenon. Similarly, if there is no target gas to be measured and the long-time drift is smaller than 2% of the maximum range, it is a normal scope. Meanwhile, it is necessary to confirm whether there are gases to be detected onsite or whether the gas and moisture fluctuations in the air are huge, thus causing numerical instability. Under general conditions, dramatic fluctuations of humidity and moisture can cause serious fluctuations of the detection value. After the temperature and moisture in the air becomes constant, the numerical value will become relatively steady.
Confirm whether it is necessary to calibrate the zero point or the target point. If there is target gas to be measured, zero-point calibration might fail to detect the low-concentration gas. If the target-point calibration is conducted under the condition of with the target gas to be measured, the calibrated concentration value and the actually measured concentration value might be inconsistent with each other. Finally, the numerical fluctuations of the instrument or the measured value might be small. These two conditions both restore factory settings.
If the above problems cannot yet get addressed, it should be confirmed whether there is high-concentration gas pumped into the gas detector or there is high-concentration gas impacting the sensor. If in the latter’s condition, the instrument should be left aging for 24 hours after getting powered on. If the reading is still unstable, the sensor might be damaged by the impact.
Fault 3: Inaccurate detection
Solution: Confirm whether the onsite gas concentration is accurate. Sometimes, the theoretical value and the actually measured value might be far apart from each other. Under the condition, the standard gas should be pumped in to verify the instrument's accuracy, or be sent to the third-party measurement instrument for detection.
If the sensor is used for a long time, the measured value might have certain error. It is necessary to confirm with the plant about whether the sensor can be used continuously. If the service life of the sensor is nearly expired, the sensor might be serviceable after completion of calibration, and the sensor would be unable to use for a long time. Then, it is suggested that a new sensor should be adopted.
Fault 4: When the reading is zero or when the value has not yet reached the alarm level, an alarm will be raised.
Solution: Check whether the alarm value is modified. Check whether the alarm mode is modified.
Check whether the alarm state is a concentration alarm or a fault alarm. In terms of a concentration alarm, the AL or AH patterns will appear, and the red indicator light will flicker. In terms of fault alarm, the yellow light will flicker.
Solution: Check whether the pump works and whether there are minor vibrations when the pump works normally. Use the finger to block the outlet for two seconds and one can perceive obvious suction. Then, check whether the inlet of the filter is blocked or whether the connection fails to ensure good sealing, thus resulting in gas leakage and lack of suction.
Pump in the ammonia gas to calibrate the zero point or calibrate the zero point in the clean water. Immediately detect after calibration.
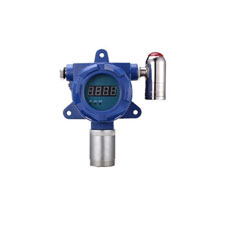
If the gas cannot yet be detected after zero-point detection, the ex-factory setting should be restored.
If the gas cannot be detected even after recovery of the ex-factory setting, the nitrogen can be pumped in or the zero-point calibration can be conducted in the clean air. Detect immediately after calibration.
Detect whether the connection line of the sensor is manually damaged or poorly connected. If the gas cannot yet be detected after all the above steps, you should confirm whether there are other gases detected onsite or whether the concentration of the detected gases is very low. If the concentration is lower than the lower limit, the target gas would be unable to detect.
Fault 2: There are no target gases to be detected in the air, but there are huge fluctuations or chaotic bounces.
Solution: That the zero-point fluctuation is smaller than 1% of the maximum range for a short period of time is a normal phenomenon. Similarly, if there is no target gas to be measured and the long-time drift is smaller than 2% of the maximum range, it is a normal scope. Meanwhile, it is necessary to confirm whether there are gases to be detected onsite or whether the gas and moisture fluctuations in the air are huge, thus causing numerical instability. Under general conditions, dramatic fluctuations of humidity and moisture can cause serious fluctuations of the detection value. After the temperature and moisture in the air becomes constant, the numerical value will become relatively steady.
If the above problems cannot yet get addressed, it should be confirmed whether there is high-concentration gas pumped into the gas detector or there is high-concentration gas impacting the sensor. If in the latter’s condition, the instrument should be left aging for 24 hours after getting powered on. If the reading is still unstable, the sensor might be damaged by the impact.
Fault 3: Inaccurate detection
Solution: Confirm whether the onsite gas concentration is accurate. Sometimes, the theoretical value and the actually measured value might be far apart from each other. Under the condition, the standard gas should be pumped in to verify the instrument's accuracy, or be sent to the third-party measurement instrument for detection.
If the sensor is used for a long time, the measured value might have certain error. It is necessary to confirm with the plant about whether the sensor can be used continuously. If the service life of the sensor is nearly expired, the sensor might be serviceable after completion of calibration, and the sensor would be unable to use for a long time. Then, it is suggested that a new sensor should be adopted.
Fault 4: When the reading is zero or when the value has not yet reached the alarm level, an alarm will be raised.
Solution: Check whether the alarm value is modified. Check whether the alarm mode is modified.
Check whether the alarm state is a concentration alarm or a fault alarm. In terms of a concentration alarm, the AL or AH patterns will appear, and the red indicator light will flicker. In terms of fault alarm, the yellow light will flicker.
Post a Comment:
You may also like: